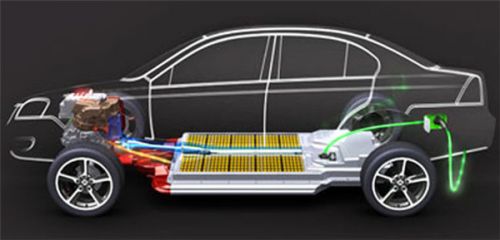
Electric vehicles use electric energy instead of fossil fuels as the power, and are the only long-term solution for future transportation. As the heart of electric vehicles, the power battery system can only realize the smooth promotion of electric vehicles only if it is fully understood. This paper focuses on the development trend of lithium-ion batteries and their battery management systems from the perspective of the development trend of main vehicle power batteries for electric vehicles at home and abroad.
Lithium-ion battery pack chargers are not balanced enough to cause overcharge and discharge problems, which seriously damage their service life. This paper proposes a new intelligent charger charging mode, which makes the battery pack safer and more reliable to charge the charger, which can extend its service life, increase safety and reduce the cost of use.
1. Car lithium ion battery management system
As the monitoring "brain" of electric vehicle batteries, the battery management system (BMS) can monitor the remaining battery power in hybrid electric vehicles, predict the power intensity of the battery, and facilitate the understanding of the entire battery system and the control of the vehicle system. .
In pure electric vehicles, the BMS has intelligent adjustment functions such as predicting remaining battery power, predicting mileage, and troubleshooting. BMS is particularly effective for lithium-ion batteries, which can improve battery usage, extend battery life, and increase battery safety. BMS will be the key technology for the future development of electric vehicles.
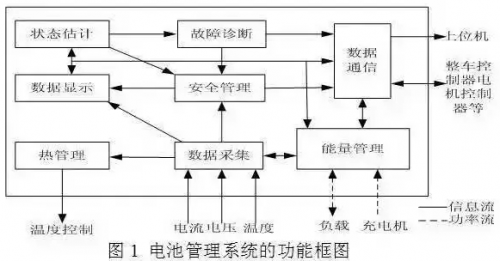
As shown in Figure 1, the data acquisition module in the BMS measures the voltage, current, and temperature of the battery pack, and then transmits the collected data to the thermal management module and the security management module for data display. The thermal management module controls the battery cell temperature to ensure that the battery pack is within the optimal temperature range.
The safety management module judges the voltage, current, temperature and state of charge (SOC) estimation results of the battery pack, and issues a fault alarm when a fault occurs and promptly takes an emergency protection measure such as an open circuit. The state estimation module performs SOC and health state (SOH) estimation based on the collected battery state data.
At present, it is mainly SOC estimation, and the SOH estimation technology is still not mature. The energy management module controls the charging and discharging process of the battery, including battery power balance management, which is used to eliminate the inconsistency of the power of each unit in the battery pack. The data communication module adopts the way of CAN communication to realize communication between the BMS and the in-vehicle device and the off-board device.
The core functions of BMS are SOC estimation, balance management and thermal management. In addition, it also has other functions such as charge and discharge management, precharger charge management and so on. During the charging and discharging process of the battery, it is necessary to manage according to the environmental parameters, battery status and other related parameters, and set the optimal charging and discharging curve of the battery, for example, setting the charging current of the charging device, the charging upper limit voltage value of the charger, and the lower limit voltage value of the discharging. The capacitive load of the high-voltage system circuit of an electric vehicle is equivalent to a short circuit at the moment of power-on, so pre-charger charging management is required to prevent the transient current surge on the high-voltage circuit.
2, the core function of the battery management system
2.1 SOC estimation
The SOC is used to describe the remaining battery power and is one of the most important parameters in the battery life. The SOC estimation is the basis for judging the overcharge and overdischarge of the battery. The accurate estimation can avoid the problem of overcharge and discharge of the battery pack to the maximum extent, so that it can operate more reliably.
The estimation of the battery SOC exhibits a very strong nonlinearity under the influence of the internal working environment and the external environment change. There are many internal and external factors that affect the battery capacity, such as battery temperature, battery life, battery internal resistance, etc. It is very difficult to accurately complete the SOC estimation.
The existing SOC estimation methods are as follows:
(1) An hour measurement method. The Anshi measurement method does not consider the changes in the internal structure and state of the battery, and thus has the advantages of simple structure and convenient operation, but the accuracy of the method is not high. If the current measurement accuracy is not high, then as time goes by, the SOC cumulative error will continue to increase, affecting the final result. The method is suitable for measuring the battery SOC on an electric vehicle. If the measurement accuracy can be improved, it is a simple and reliable SOC measurement method.
(2) Open circuit voltage method. The open circuit voltage of the lithium ion battery has an approximately linear relationship with the SOC, which can be used to determine the internal state of the battery. However, due to the strict measurement requirements, the battery needs to be placed for at least 1 h. It is not suitable for online real-time detection of batteries in electric vehicles. Under normal circumstances, due to the open circuit voltage method, the accuracy of the initial and final estimates of the charging of the charger is relatively high, and the open circuit voltage method is often used in combination with the ammeter measurement method.
(3) Kalman filtering method. The Kalman filter method is especially suitable for hybrid batteries with high current fluctuations due to its excellent correction error capability. The disadvantage of this estimation method is that it requires high processing speed of the system.
(4) Neural network method. Neural networks have features such as distributed parallel processing, nonlinear mapping, and adaptive learning, so they can be used to simulate battery dynamics and estimate SOC. However, this method requires a large amount of reference data for the neural network to learn, and the data and training methods are required to be high, otherwise unacceptable errors will be caused.
2.2 Balance Management
There are many processes in the process of producing a battery, and differentiation can cause inconsistencies. The difference in battery cells is mainly reflected in the change in internal resistance and capacity over time and temperature. Large differences between cells are more likely to cause overcharge or overdischarge, resulting in battery damage. Achieving battery balance maximizes the utility of the power battery, extending battery life and increasing safety. At this stage, the mainstream balance methods at home and abroad are as follows:
(1) Resistance equalization method. This method is the main representative of the energy dissipation type equalization method. The method is simple and the cost is low, but the energy loss is relatively large and the efficiency is low. It is only suitable for systems with small current charge and discharge.
(2) Switched capacitance method. This method is the main representative of the non-energy dissipative type equalization method, which makes up for the shortcomings of resistance equalization. However, its control circuit is complicated, the equalization speed is slow, and it takes a long time, which is not suitable for large current use.
(3) Transformer equalization method. This method is based on a symmetrical multi-winding transformer structure of a series battery pack active equalization control method. Its shortcomings are complicated circuits, many devices, and too large a volume, which is not easy to expand the battery pack. Generally suitable for charging and discharging of large currents.
(4) Centralized equilibrium. The method can quickly transfer the entire battery pack to the battery cells, and the centralized equalization module is smaller in size. However, the balancing operation of multiple batteries cannot be performed in parallel, and a large number of cable connections are required, which is not suitable for a battery pack having a large number of batteries.
2.3 Thermal management
Temperature has an impact on all aspects of battery performance. Temperature field non-uniformity will exacerbate the inconsistency of the battery pack, so it is necessary to manage it. The purpose of thermal management is to maintain the temperature of the battery system within a certain range by heating or heat dissipation, and to maintain the temperature uniformity within the battery as much as possible.
Temperature management mainly completes the following four functions: (1) rapid heating of the battery pack under low resistance conditions; (2) ensuring uniform distribution of the battery temperature field; (3) accurate measurement and monitoring of the battery temperature; (4) in the battery pack When the temperature is too high, the amount of heat is effectively dissipated. Commonly used cooling methods include natural convection method, forced air convection method, liquid flow method, phase change material method and thermal management method. Common heating methods include battery internal heating method, heating plate method, heating jacket method and heat pump method.
3, lithium ion battery charger charging technology
3.1 Status and development trends
In practical applications, selecting different charger charging modes according to battery capacity limits is an inevitable choice to extend battery life. Lithium-ion battery chargers have more charging methods, the simplest is the constant voltage charger charging method. Lithium-ion battery packs generally consist of a large number of monomers connected in series. Due to the difference in manufacturing process of each monomer, there are inconsistencies in internal resistance, voltage, capacity and temperature, which may cause imbalance in the process of charging and discharging, that is, large-capacity singles. The body is shallow and the small capacity unit is over-discharged, which will cause serious damage to the battery pack. Solving the problem of unbalanced charging and discharging is the research focus of lithium-ion battery packs.
The requirements for electric vehicle charging technology for battery chargers include:
(1) The charger charging process is fast. The low power ratio of the power battery leads to a short cruising range of the one-time charger, which has been an important factor limiting the development of electric vehicles. As long as the battery is charged faster and more efficiently, it can indirectly compensate for the weakness of the short range of electric vehicles.
(2) The charging device of the charger is generalized. In order to pursue relevant academic frontiers and optimize their products to gain as much market share as possible, various new types of batteries have emerged in an endless stream and coexist in this market. In the case where batteries of different types and different voltage levels coexist, the charging device of the charger in the public place needs to have wider adaptability. On the one hand, the charger of the charger needs to be applied to as many batteries as possible, and on the other hand, for different batteries. Voltage level, charger chargers need to meet customer requirements.
(3) The charger charging strategy is intelligent. In order to realize the charging of the non-destructive charger of the battery as much as possible, monitor its charging and discharging state, avoid over-discharging, achieve the purpose of energy saving and delay aging, and need a smarter charging strategy of the charger. That is, different charger charging strategies are provided for different batteries to match the battery charger charging curve.
(4) Efficient power conversion. The energy loss of electric vehicles is closely related to the operating cost. In order to further promote electric vehicles, it is necessary to balance their cost performance and reduce energy consumption.
(5) The charger charging system is integrated. With the requirements of system miniaturization and multi-functionality, as well as the improvement of battery reliability and stability requirements, the charger charging system will be integrated with the electric vehicle energy management system as a whole, integrating current detection and reverse discharge protection. A smaller, more integrated charger charging solution can be realized without external components, saving space for the rest of the electric vehicle, greatly reducing system cost, optimizing charger charging and extending battery life.
3.2 Smart Charger Charging Technology
Based on the above analysis of the current status of charging lithium-ion battery packs and their chargers, this paper summarizes an intelligent charger based on electric vehicle BMS for the imbalance and safety problems in the charging process of lithium-ion battery pack chargers. Charging mode, as shown in Figure 2.

During the charging process of the charger, the BMS system mainly monitors the voltage and current signals of the lithium-ion battery pack, and detects the temperature and connection status. The intelligent management system in the charger of the charger is for the output mode of the charging device of the charger. Real-time monitoring. The BMS system and the charging device charging device intelligent management system realize intelligent communication, perform real-time mode comparison between the battery pack and the charging device charging device state, and select an optimal charging mode for the battery pack.
During the initial charging process of the charger, BM


ZGAR Disposable Vape
ZGAR electronic cigarette uses high-tech R&D, food grade disposable pod device and high-quality raw material. All package designs are Original IP. Our designer team is from Hong Kong. We have very high requirements for product quality, flavors taste and packaging design. The E-liquid is imported, materials are food grade, and assembly plant is medical-grade dust-free workshops.
Our products include disposable e-cigarettes, rechargeable e-cigarettes, rechargreable disposable vape pen, and various of flavors of cigarette cartridges. From 600puffs to 5000puffs, ZGAR bar Disposable offer high-tech R&D, E-cigarette improves battery capacity, We offer various of flavors and support customization. And printing designs can be customized. We have our own professional team and competitive quotations for any OEM or ODM works.
We supply OEM rechargeable disposable vape pen,OEM disposable electronic cigarette,ODM disposable vape pen,ODM disposable electronic cigarette,OEM/ODM vape pen e-cigarette,OEM/ODM atomizer device.
Disposable E-cigarette, ODM disposable electronic cigarette, vape pen atomizer , Device E-cig, OEM disposable electronic cigarette
ZGAR INTERNATIONAL TRADING CO., LTD. , https://www.szvape-pen.com