At all levels of the network, automation and control engineers are increasingly dealing with networking challenges as their demands for connectivity grow. Ethernet and Industrial Ethernet are evolving to better suit factory environments, with OEMs continuously offering products that support higher frequencies and more advanced functionalities. As these technologies develop, Ethernet is likely to simplify to just one layer—cables and connectors—while serving a wide range of industrial needs through a unified network.
In monitoring and data acquisition applications, engineers have widely adopted Ethernet protocols in SCADA systems, factory diagnostics, testing, and maintenance. Commonly used protocols include TCP/IP and EtherNet/IP. Collaboration between engineering teams and IT departments is essential for system integration. A recent survey by ControlEngineering and ReedResearchGroup highlighted current and future usage trends among factory and OEM professionals, revealing how Ethernet and Industrial Ethernet are shaping modern industrial communication.
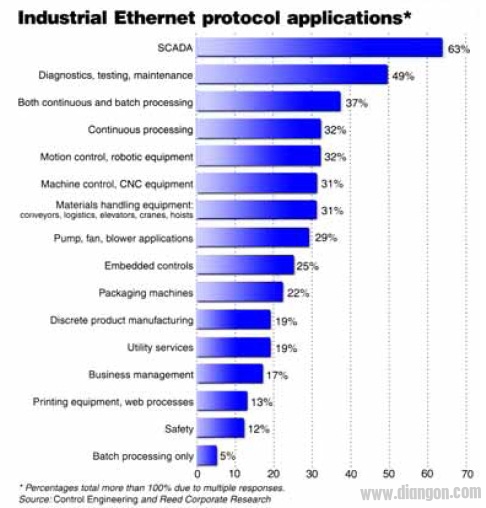
Figure 1: The Ethernet protocol has multiple uses in the factory, primarily in data acquisition and monitoring (SCADA), diagnostics, detection, and maintenance.
Patterns of Use
A survey was conducted on 263 customers who ordered, recommended, or purchased Ethernet protocols and products. Over 19% of respondents applied both in factory and OEM settings, while 51% used it exclusively for factory purposes. More than 30% used it only for OEM requirements. One-third of respondents had not yet formed a cross-functional team, but those who did often included 60% engineers, 30% from IT, 28% from plant engineering, and 20% from production and management.
When asked about their use of Industrial Ethernet, 63% used it for SCADA, 49% for diagnostics, 37% for continuous and batch processing, 32% for motion control, and 31% for logistics equipment. Most users (88%) use Ethernet for monitoring or data collection, 84% for control, and 63% for I/O data transmission.
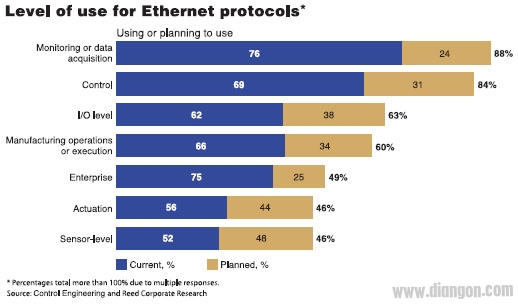
Figure 2: The most common applications for Ethernet protocols are monitoring/data acquisition and control.
Respondents also mentioned enterprise applications and sensor integration. Current and planned Ethernet connections include network hardware (79%), PLCs (78%), and PCs (77%). Among these, 84% of network devices are already connected, with 16% planning to connect within 12 months. Similarly, 80% of PLCs are connected, and 20% plan to connect soon. Other applications like I/O systems and PACs are also growing in popularity.
When choosing Ethernet protocols for industrial use, 73% of respondents selected TCP/IP and EtherNet/IP, while 47% chose ModbusTCP. Other protocols like UDP (23.6%), Profinet (20%), and HSE (20%) were also popular. Protocols like SERCOSIII (11.1%), EtherCAT (10.6%), and Ethernet Powerlink (8%) had smaller shares. Almost all respondents (99%) found speed, compatibility, and device availability important features.
Over 88% of respondents reported using Industrial Ethernet, with nearly all (99%) being satisfied. About one-third started using it 2–5 years ago, while 25% began 6–10 years ago. 14% have been using it for over 10 years, and 12% plan to implement it within two years.
TCP/IP dominates industrial Ethernet, with 73% of users adopting or planning to adopt it. It's a foundational protocol for internet communication, and its evolution continues under the IETF. The IETF maintains and updates TCP/IP to ensure smooth operation, including security enhancements and performance improvements.
EtherNet/IP, part of the CIP family, is also widely used. It supports real-time control and integrates well with standard protocols like OPC. With its flexibility and compatibility, it enables seamless communication across various industrial applications.

Figure 3: Ethernet/IP follows the OSI model, similar to other CIP networks.
Modbus/TCP is another popular choice, with 48.5% of users adopting it. It’s open, cost-effective, and compatible with TCP/IP, making it ideal for data exchange. Users can easily integrate devices with minimal hardware and no licensing fees.
UDP is used by nearly a quarter of users for transaction-oriented tasks. While it doesn’t guarantee reliability, it offers fast, lightweight communication, suitable for time-sensitive applications where some data loss is acceptable.
HSE (High-Speed Ethernet) is used by 20% of respondents. It’s designed for mission-critical applications and supports complex logic functions and high-speed data transfer. It’s an international standard and works with various fieldbus technologies.
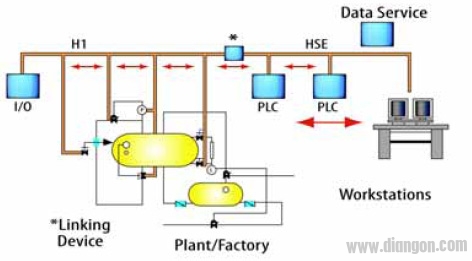
Figure 5: HSE is ideal for control hubs and supports many fieldbus features.
Profinet, used by 20% of respondents, is known for its versatility. It integrates with various fieldbuses and supports wireless communication. It’s suitable for motion control, security, and vertical integration, and is supported by the PI organization.
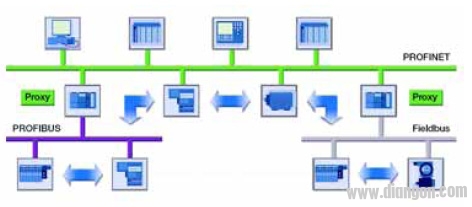
Figure 6: Profinet absorbs other fieldbuses like DeviceNet and Modbus.
SERCOS III, used by over 11%, is a real-time protocol for motion control. It supports high-speed communication, synchronization, and fault tolerance, making it ideal for demanding industrial environments.
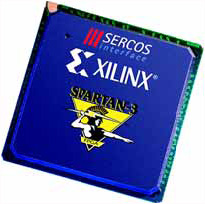
Figure 7: FPGA-based controllers using SERCOS III for real-time motion control.
As industrial networks continue to evolve, the choice of protocol becomes crucial. Whether it’s TCP/IP, EtherNet/IP, Modbus/TCP, or others, each protocol brings unique advantages to different applications, ensuring efficient and reliable communication in modern manufacturing environments.
round Installation Antenna,Gy06 Military Green Log Periodic Antenna,Gy06 Military Green Antenna Internal Antenna
Mianyang Ouxun Information Industry Co., Ltd , https://www.ouxunantenna.com