At all levels of the network, automation and control engineers are increasingly dealing with networking challenges. As their needs grow, so do the expectations for more advanced and flexible solutions. Ethernet and Industrial Ethernet have become essential in factory environments, adapting to various applications through continuous technological improvements. OEMs are now offering products with higher frequencies and better performance, making Ethernet a versatile choice for both basic and complex systems.
In monitoring and data acquisition systems, Ethernet protocols like TCP/IP and EtherNet/IP are widely used. Engineers often collaborate with IT departments to design integrated systems that meet both operational and informational needs. A recent survey by ControlEngineering and ReedResearchGroup highlighted the growing adoption of Ethernet in manufacturing and OEM settings, showing that many companies are already leveraging these technologies or planning to do so soon.
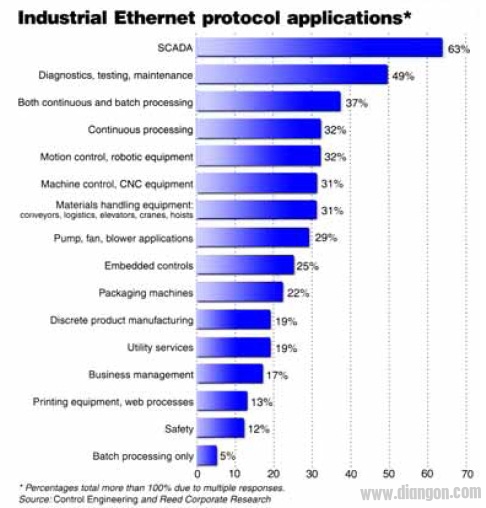
Figure 1: The Ethernet protocol has a variety of uses in factories, primarily for data acquisition, monitoring, diagnostics, and maintenance.
Patterns of use show that over 19% of respondents apply Ethernet in both factory and OEM settings, while 51% use it exclusively in factory environments. Many companies still rely on OEMs for specific network requirements. Cross-functional teams are becoming more common, with engineers forming the majority (60%), followed by IT (30%), plant engineering (28%), and production management (20%).
When asked about their use of Industrial Ethernet, most respondents cited SCADA systems (63%) and diagnostics/testing (49%). Other key applications include continuous and batch processing (37%), motion control (32%), and CNC equipment (31%). These trends highlight the increasing integration of Ethernet into core industrial operations.
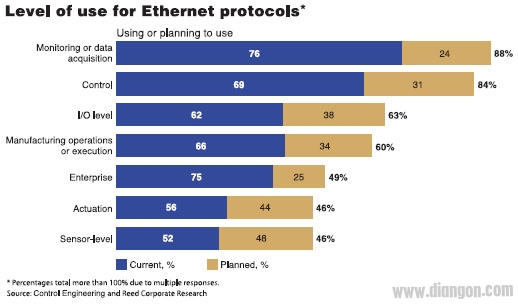
Figure 2: The most common applications for Ethernet are data acquisition, monitoring, and control.
Most users (88%) use Ethernet for monitoring or data collection, 84% for control, and 63% for I/O communication. Many also use it for production operations, enterprise applications, and sensor integration. Network hardware (79%), PLCs (78%), and PCs (77%) are the primary devices connected via Ethernet. A significant portion of respondents plan to expand their network infrastructure within the next year.
Among the top Ethernet protocols, TCP/IP and EtherNet/IP lead with 73% of respondents using them. ModbusTCP follows at 47%, while UDP, Profinet, and HSE each account for around 20%. Other protocols such as SERCOSIII, EtherCAT, and Ethernet Powerlink have smaller but notable shares. This diversity reflects the need for flexibility in different industrial scenarios.
Industrial Ethernet is widely adopted, with 88% of respondents using it in their factories. Almost all (99%) are satisfied or very satisfied with its performance. Many have been using it for several years, and a growing number plan to implement it within the next two years. Speed remains the most critical feature, with 94% of users requiring high-speed capabilities.
Other important features include compatibility with existing Ethernet devices (86%), support for 10/100BaseT/TX (86%), and availability of off-the-shelf components (85%). Additional features such as scalability (79%), security (79%), and real-time data transfer (77%) are also highly valued. These factors contribute to the ongoing popularity of Ethernet in industrial settings.
Many engineers (58%) handle Industrial Ethernet installations themselves, while others rely on third-party integrators or consultants. Understanding which protocol to use is crucial, with 60% of respondents knowing their needs and 27% considering themselves experts in this area.
TCP/IP, though not originally designed for industrial use, dominates the market. It is a foundational protocol for internet communication and is continuously maintained and updated by the IETF. Its widespread adoption is due to its reliability, flexibility, and compatibility with other systems.

Figure 3: Ethernet/IP architecture follows the OSI model and supports real-time control.
EtherNet/IP is a popular choice among 73% of respondents. It is part of the CIP family and supports real-time control, synchronization, and data exchange. It is compatible with standard Ethernet and can integrate with other protocols like OPC. Its versatility makes it ideal for industrial automation and control systems.
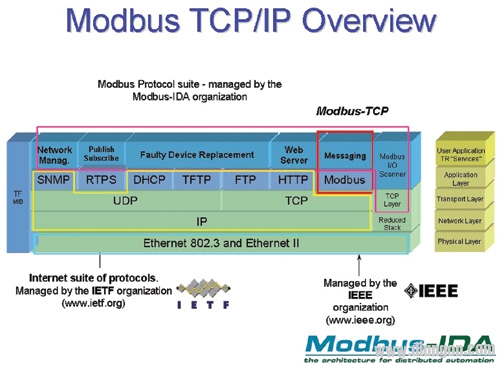
Figure 4: Modbus is a scalable and open protocol suitable for various applications.
Modbus/TCP is widely used, with 48.5% of respondents adopting it. It combines Ethernet with TCP/IP and offers a vendor-neutral approach. It is easy to implement and free to use, making it a popular choice for industrial networks. Its simplicity and flexibility allow for quick integration with existing systems.
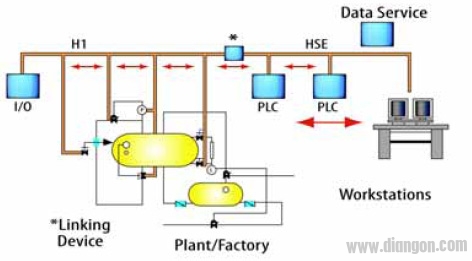
Figure 5: HSE is ideal for mission-critical control applications and supports advanced fieldbus features.
High-Speed Ethernet (HSE) is used by 20% of respondents. It is designed for high-performance control and integrates with existing fieldbus technologies. It supports complex logic functions and is suitable for process and discrete manufacturing. HSE is an international standard (IEC61158) and ensures seamless communication between different vendors' devices.
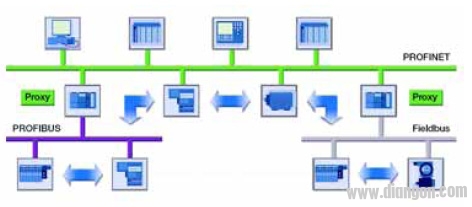
Figure 6: Profinet supports multiple fieldbuses and is ideal for comprehensive automation.
Profinet is another major protocol, used by 20% of respondents. It supports a wide range of applications, from discrete to process automation. It works on wireless Ethernet and allows for real-time control of mobile devices. Profinet integrates with existing Profibus networks and provides a secure, scalable solution for modern factories.
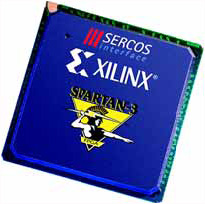
Figure 7: SERCOS III supports high-speed motion control and real-time communication.
SERCOS III is used by over 11% of respondents. It enhances motion control and real-time communication, supporting up to 150 axes with sub-millisecond precision. It reduces cycle times and improves system efficiency, making it ideal for demanding applications like printing and packaging. Its use of standard Ethernet and FPGA-based controllers makes it cost-effective and scalable.
High Gain panel antenna,outdoor high gain antenna,high gain indoor antenna
Mianyang Ouxun Information Industry Co., Ltd , https://www.ouxunantenna.com