1 Traditional digital PID algorithm
1.1 Positional Control Algorithm
The positional PID control algorithm is described as:

make


Where: k - the sampling number;
u(k) - the calculation result of the kth sampling time;
e(k) - the deviation of the first sampling from the target position;
Kl - integral coefficient;
KD - differential coefficient;
KP - scale factor;
TI - integral time constant;
TD - differential time constant;
T - sampling period.
It can be seen from equation (2) that each output is related to the past state. To calculate u(k), not only e(k-1), but also the previous additions. Therefore, using equation (2) to calculate complexity, wasting memory. When the control is switched from manual to automatic, the output value of the computer must be set to the original valve opening uD to ensure no impact switching.
1.2 Incremental Control Algorithm
The incremental PID control algorithm is described as:
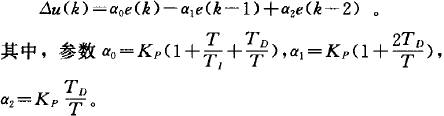
Incremental calculation only needs to calculate the increment. When there is calculation error or insufficient precision, the influence on the control quantity calculation is small. Since uO does not appear in the calculation, manual-to-automatic bumpless switching is easy to implement. In addition, in the event of a computer failure, the actuator itself can remain in place due to the registration function itself.
Based on the above two conventional algorithms, we have proposed a number of improved algorithms in practical applications. In this project, the integral separation PID control algorithm is adopted.
2 integral separation PID algorithm
The mathematical model of the integral separation control algorithm is as follows:
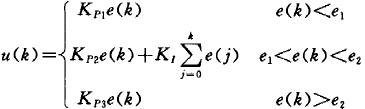
Among them, e1 and e2 respectively represent the left and right intervals, that is, the distance from the target position, which is a conventional integral separation PID control algorithm. In actual applications, segmentation can be performed again according to different systems and actual conditions. 3 Algorithm in position servo system
In the system we studied, the method used was multiple integral separation and integral separation during forward and reverse overshoot.
First, we will describe the mathematical model of the parameter tuning used. The segmentation is shown in Figure 1.
Figure 1 segment circle
In Fig. 1, 1 and 7 indicate that there are positive and negative points in the full speed motion section. Right is positive, left is negative; 2 and 6 respectively indicate the left and right intervals of the target position using the pure proportional adjustment control; 3 and 5 respectively represent the part that needs to use the conventional PID algorithm; 4 means use within a small error range Proportional integral control.
The above segmentation is a segmentation for the actual system. It is a segmentation method suitable for this system. It not only meets the requirements in terms of speed and accuracy, but also is more suitable for this system than other methods we have used.
4 parameter setting
Since the system we studied is a system with higher position accuracy requirements, the tuning requirements for the parameters are relatively high. On the basis of continuous experiment, a set of methods suitable for the system to obtain parameters by approximate calculation is summarized.
Since the system is a follow-up system, it is difficult to establish a precise mathematical model of the system. Only the amplification factor of the forward channel is N, the motor saturation voltage is U1, and the maximum speed of the motor is v1. The tuning of the position loop parameters affects the accuracy and rapidity of the whole system. Based on the continuous experiment, we summarize the following methods:
(1) Perform corresponding segmentation on the system. Segmentation is determined experimentally. Since the system itself is a complex nonlinear high-order system, segmentation is an important part. The step response of the system under different conditions is continuously tested through experiments. in accordance with.
(2) Determine the parameters of the last algorithm part. We use different PID algorithms for different positions, in which the voltage of the turning part is a relatively important parameter. According to the experiment, we determine that the voltage output by the algorithm is multiplied by the amplification factor of the previous path as the voltage value applied to the motor. Of course, this voltage must be such that the motor still has speed under load.
(3) Determine the scale factor of the 2 and 6 segments. The proportional coefficient here is obtained by the voltage and displacement of the two turning points, which is a linear function relationship, that is, U output = KPS displacement. Among them, the U output is the output part of the algorithm; KP is the proportional coefficient of 2 segments and 6 segments; the S displacement is the displacement amount relative to the target position. A set of U outputs, S displacements can be obtained by the transition between 1 and 2 or 6 and 7, and another set of U outputs, S displacements can be obtained by the transition between 2 and 3 or 5 and 6. Determine KP.
(4) Determine the PID parameters of the fourth paragraph. From the voltage value of the turning portion obtained above, we have the starting voltage, and based on the obtained starting voltage, the proportional coefficient can be determined. When determining this proportionality factor, the integral and differential coefficients must be made zero. Through the determination of this proportional coefficient, we can completely calculate the required parameters. In order to meet the accuracy requirements, the adjustment of the parameters can be completed by adding appropriate integral terms according to experience. Note that the smaller the integral term is added, the better, of course, within the guaranteed accuracy range.
5 Conclusion
Experiments have shown that the motion process we get meets the requirements of speed and accuracy. The solution summarized in the experiment is feasible and reasonable.
Water cooling computer kit is a package that launched by the manufacturer, one kind is all water cooling accessories, players purchased and according to individual case to install, other kind is that manufacturer provide the full suit which including computer hardware and water cooling accessories. manufacturer will provide many varies of solutions for buyers to choose, in particular case, buyers can customized produce according to the personal preference. In a word, water-cooling kit simplifies the process of players using a water cooling computer,they can enjoy water cooling computer faster and more convenient.
Computer Water Cooling Kits,Water Cooling Computer Kits,Diy Water Cooling Computer Kits,Colorful Cooled Computer Kits
Dongyuan Syscooling Technology Co., Ltd. , http://www.syscooling.com